We consistently encounter a plastic recycling emblem featuring a triangular arrangement of arrows at the base of the takeaway containers and plastic bottles we utilize daily.
The symbols marked with “1” for PET and “5” for PP are notably common, and this observation is easily made.
What are the distinguishing characteristics of these two types of materials? Could you elucidate the differences between them? Additionally, which material is superior?
The forthcoming content will conduct a technological investigation on “PP vs. PET” to seek solutions to these inquiries.
A Comprehensive Overview of Polypropylene
Polypropylene, abbreviated as PP, is a thermoplastic resin synthesized through the polymerization of propylene.
The material possesses a melting point of 167 degrees Celsius and exhibits a clean, light, waxy white look.
Polypropylene is a highly crystalline, non-toxic, odorless, and tasteless polymer. It possesses a milky white hue and a density of approximately 0.90–0.91 g/cm³, rendering it one of the lightest varieties of plastics.
Polypropylene is categorized into three unique varieties: isotactic polypropylene, atactic polypropylene, and syndiotactic polypropylene, each differentiated by the configuration of the methyl groups.
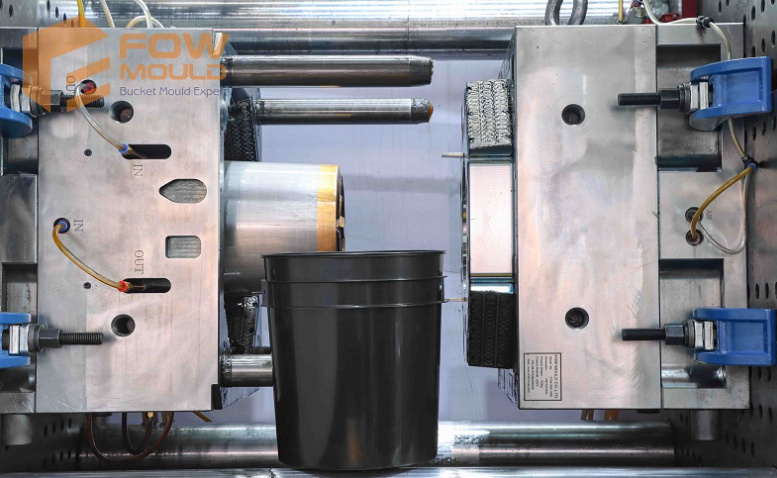
What is the PET?
The polyester family of polymers comprises polybutylene terephthalate (PBT) and polyethylene terephthalate (PET or PETE). This group of polymers is commonly designated as thermoplastic polyester, frequently termed saturated polyester.
The production of this substance employs two methods: the transesterification of dimethyl terephthalate with ethylene glycol and the synthesis of bis-hydroxyethyl terephthalate via the esterification of terephthalic acid with ethylene glycol, succeeded by a polycondensation reaction.
This polymer typically exhibits a milky white or light yellow hue, is highly crystalline, and possesses a smooth, glossy surface.
This resin is commonly found in daily life and can be categorized into three distinct types: APET, RPET, and PETG.
What are the physical and chemical properties of polypropylene (PP) and polyethylene terephthalate (PET)?
Before assessing the quality of a material, it is essential to first comprehend its characteristics.
Consequently, let us commence by delineating the characteristics of PP and PET from multiple viewpoints, including:
Mechanical properties
Polypropylene exhibits exceptional stiffness and resistance to flex fatigue. Despite its poor impact strength at reduced temperatures, polypropylene (PP) hinges may last over seventy million folding cycles without exhibiting any evidence of fracture.
PET, conversely, is the thermoplastic that exhibits the maximum degree of toughness, minimal wear, and significant hardness. The material has adequate creep resistance, fatigue resistance, and dimensional stability.
Attributes of Warmth
Polypropylene is a thermally resistant substance.Sterilization of polypropylene injection-molded products is feasible at temperatures exceeding 100 degrees Celsius.
At a temperature of 150 degrees Celsius, they remain undeformed in the absence of external forces.
PET can endure heat effectively, maintaining its physical and mechanical properties throughout a wide temperature spectrum, with a service temperature of up to 120 degrees Celsius.
The stability of chemical compounds
Polypropylene is an exceptionally chemically stable material. The majority of chemicals are inert to it, save for concentrated sulfuric acid and nitric acid, which induce its degradation.
Conversely, it may expand when subjected to specific halogenated compounds, aromatics, and high-boiling hydrocarbons.
Generally, PET material exhibits resistance to organic solvents and weak acids; nevertheless, it lacks resistance to alkalis and prolonged exposure to hot water.
Electrifying Attributes
Regarding high-frequency insulation, polypropylene exhibits outstanding properties. Moreover, it maintains excellent electrical insulation in humid conditions due to its minimal water absorption.
PET exhibits excellent electrical insulating capabilities, particularly at elevated temperatures and frequencies; nevertheless, its resistance to corona discharge is inferior. This remains true despite the qualities of PET.
The Attributes of the Processing
A range of production techniques can be employed to make polypropylene plastic, including injection molding, extrusion molding, blow molding, and foaming. Polypropylene plastic exhibits advantageous processing characteristics.
The sluggish crystallization rate of PET resin results in suboptimal processing performance, necessitating adequate drying prior to forming; failure to do so may adversely affect product quality during formation.
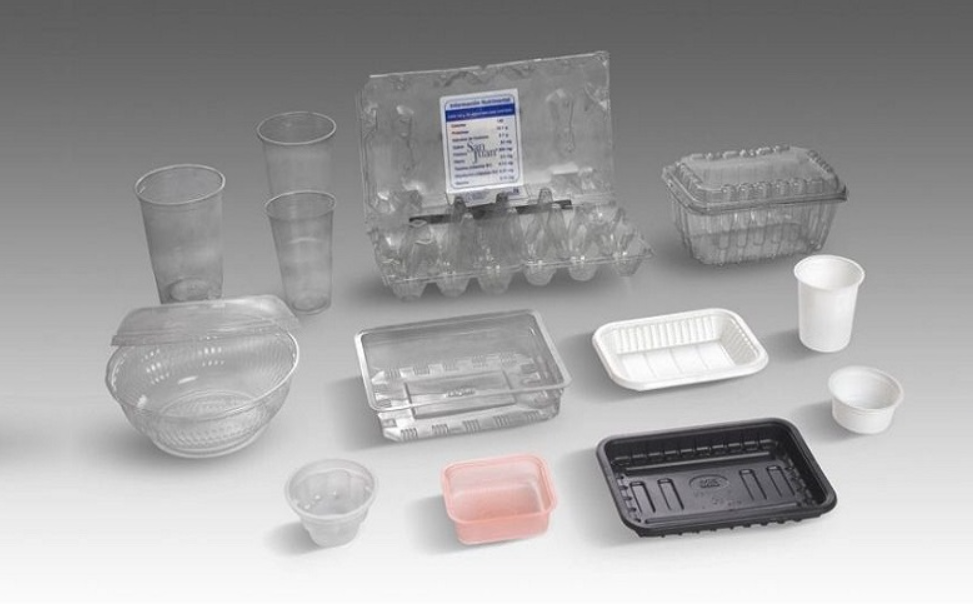
To clearly demonstrate the performance of PP and PET plastics, we have compiled a data table for your reference:
PP | PET | |
Chemical Formula | (C3H6)n | (C10H8O4)n |
Density (g/cm³) | 0.90 – 0.91 | 1.31 |
Melting Point (℃) | 164 – 170 | 250 – 255 |
Water Absorption (%) | 0.03 – 0.04 | 0.06 – 0.129 |
Tensile Strength (MPa) | 30.0 – 39.0 | 140 – 160 |
Bending Strength (MPa) | 42.0 – 56.0 | 70 – 100 |
Elongation at Break (%) | 200 – 400 | 50 – 150 |
The Advantages and Disadvantages of PP and PET
Polypropylene is esteemed for its lightweight and hygienic properties, along with its exceptional resistance to heat and chemicals. Consequently, it is suitable for medical uses and food packing.
Its susceptibility to weathering and lack of rigidity may limit its applicability in structural or outdoor contexts.
Transparent packaging that preserves the quality of consumables is an ideal application for PET, renowned for its exceptional transparency and robust barrier properties.
Although PET is recyclable and exhibits considerable mechanical strength, it is unsuitable for high-temperature applications due to its thermal sensitivity and slow crystallization rate. Furthermore, the molding process may be complicated by the material.
PP versus PET: Health and Safety Concerns
It is widely recognized that “1” PET and “5” PP are the principal materials employed in the manufacturing of commonplace plastic products, prompting worries regarding the safety of these substances: Is the use of polypropylene plastic safe? Is PET a toxic substance?
Consequently, it is imperative to do a thorough inquiry into the safety of these two elements to fully understand their effects on our health and well-being.
Polypropylene (PP) in its original form is a non-toxic, odorless, and tasteless plastic polymer generally regarded as harmless.
Polypropylene is commonly utilized for manufacturing food containers, infant bottles, and kitchen utensils since it does not leach harmful substances into food or beverages under normal usage conditions.
Conversely, PET material is safe for use at room temperature. Its transparency and stability render it an exceptional material for beverage bottles and various packaging solutions.
Polypropylene (PP) and polyethylene terephthalate (PET) are classified as food-grade polymers. Nonetheless, polypropylene remains the sole material sanctioned for microwave cooking due to its remarkable heat resistance.
PET bottles exposed to elevated temperatures, prolonged usage, or heated liquids beyond their boiling point may leach hazardous substances, including DEHP.
Consequently, exercising caution when utilizing plastic products is essential, especially concerning consumption conditions and usage duration.
The Utilization of PP and PET
In China, injection molding enterprises have historically comprised a substantial portion of the polypropylene resin utilized in the manufacturing of woven products. These goods comprise plastic weaved bags, tarpaulins, and plastic ropes.
Common applications for injection-molded polypropylene (PP) include small home appliances, daily necessities, toys, washing machines, automobiles, and turnover boxes.
Due to the exceptional properties of polypropylene fibers, its application is becoming more prevalent in décor, industry, and fashion. They are employed in the manufacturing of carpets and apparel.
Polypropylene (PP) pipes are mostly utilized in buildings, agricultural systems, and chemical pipeline systems due to its capacity to endure high temperatures, enable pipe connections, and be recycled.
Nonetheless, PET is predominantly employed in the manufacture of bottle-grade polyester, extensively used for packaging various beverages, especially carbonated drinks; polyester film, primarily utilized for packaging materials, films, and tapes; and polyester fibers for the textile sector.
Moreover, glass fiber-reinforced PET is very suitable for applications in the automotive, electrical, and electronic sectors. It is employed for various coil frameworks, electrical components, and electronic enclosures.
What Are the Distinctions Between PP and PET?
Compared to PP material, PET material is more robust, durable, and heat-resistant under standard settings.
The utilization of PET material may be more suitable for manufacturing products necessitating enhanced durability, such as bottles and jars.
Moreover, PET material exhibits greater translucency than PP material, providing a distinct advantage in the production of goods that are entirely or partially transparent.
Compared to PET, polypropylene (PP) exhibits greater malleability, reduced weight, and enhanced ease of production and molding.
Polypropylene (PP) material may be more appropriate for producing soft and lightweight items, such as apparel and bags.
Therefore, there is no conclusive answer to which material, polypropylene (PP) or polyethylene (PET), is superior; the response depends on the specific context.
Sincere Tech is one of the top 10 plastic injection molding company in China that offer all in one service from China to the worldwide, those include overmolding, insert molding, 2k molding, die casting tool and any other custom made products, we have assembly shop, if you are looking for product assembly services China partner, contact now.